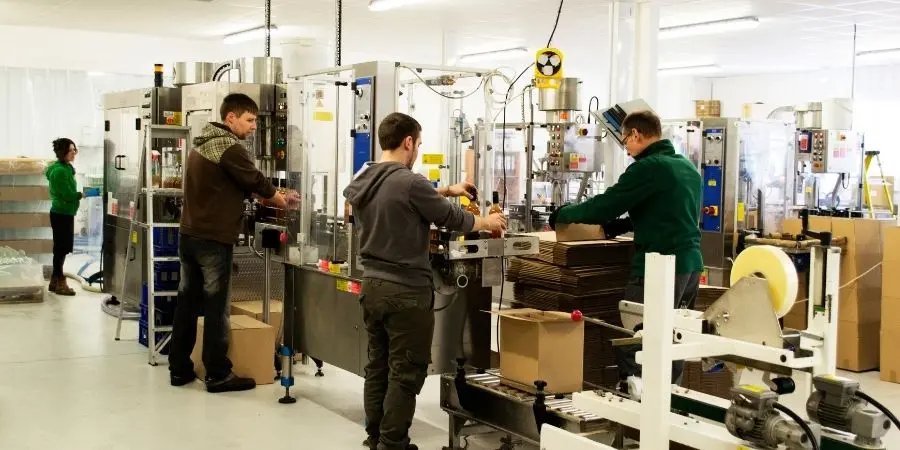
Tabla de contenido
- ¿Qué es la manufactura esbelta?
- ¿Cómo surge la manufactura esbelta?
- ¿Cuál es el objetivo principal?
- Kaizen en la manufactura esbelta
- ¿Cuáles son los 5 principios del pensamiento esbelto?
- ¿Cuáles son las herramientas de la manufactura esbelta?
- ¿Cuáles son los beneficios de la manufactura esbelta?
- Ejemplos de manufactura esbelta
- ¿Cómo aplicar la manufactura esbelta en una empresa?
- Ventajas de la manufactura esbelta
¿Qué es la manufactura esbelta?
La manufactura esbelta o lean manufacturing es una estrategia para hacer las cosas mejor.
El concepto consiste en eliminar los residuos en un sistema de fabricación aplicando prácticas que minimicen el número de pasos, recursos y mano de obra necesarios para fabricar un producto.
La manufactura esbelta también se refiere al proceso de fabricación, a menudo asociado con el Sistema de Producción Toyota (TPS), donde la producción y la calidad están en primer plano.
El TPS es un conjunto de herramientas que permiten a la organización alejarse del enfoque tradicional de “producción en masa”, consistente en producir grandes cantidades de productos similares, para pasar a un enfoque de producción “justo a tiempo”.
El TPS se creó para aumentar la productividad y reducir los costes.
¿Cómo surge la manufactura esbelta?
La idea de la manufactura esbelta existe desde hace más de 40 años. El término “manufactura esbelta” fue acuñado por primera vez por Taiichi Ohno, un profesor japonés, en la década de 1970.
Taiichi Ohno creía que, en un proceso de fabricación, la tasa de residuos era igual a la tasa de producción. La idea de la “manufactura esbelta” consistía en centrarse en la eliminación de los pasos innecesarios en el proceso de fabricación y en mejorar el flujo del proceso.
La idea central de la manufactura esbelta es centrarse en la eliminación de los pasos innecesarios, y centrarse en la mejora del flujo del proceso. El término “lean” significa “cero residuos”.
La manufactura esbelta se basa en la idea de que el proceso de fabricación debe avanzar lo más rápidamente posible, sin dejar de producir el producto correcto en el momento adecuado.
La idea de la manufactura esbelta se introdujo en un libro titulado “La máquina que cambió el mundo”, de Malcolm Clarke, en 1990.
La manufactura esbelta ha sido ampliamente aceptada como metodología para mejorar la calidad y reducir los costes de fabricación. La manufactura esbelta se ha aplicado en una amplia gama de industrias manufactureras, como la alimentaria, la química, la textil, la metalúrgica y la de maquinaria.
La fabricación esbelta ha sido ampliamente aceptada como metodología para mejorar la calidad y reducir el coste de la fabricación.
La manufactura esbelta se ha aplicado ampliamente en una amplia gama de industrias manufactureras, como la alimentaria, la química, la textil, la metalúrgica y la de maquinaria.
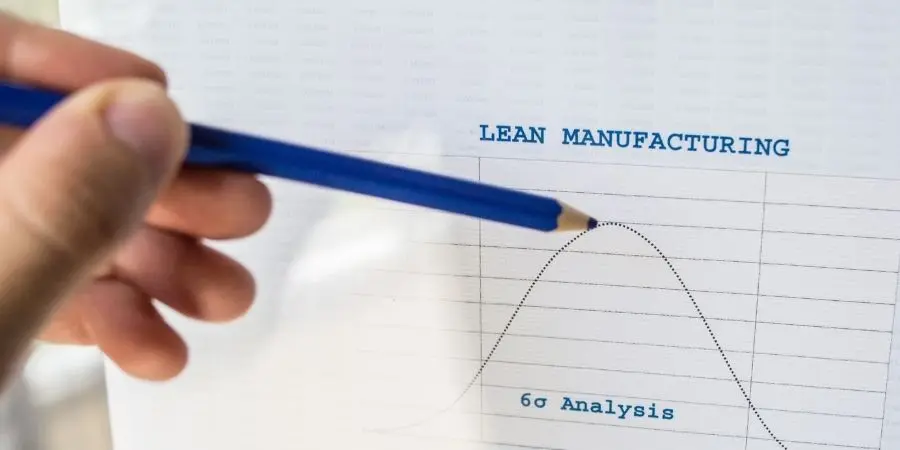
¿Cuál es el objetivo principal?
¡Productividad!
La idea de la productividad nació a principios de los años 70, cuando Estados Unidos y Japón tuvieron que cambiar su forma de hacer negocios tras el final de la Segunda Guerra Mundial.
Lo hicieron analizando sus procesos de fabricación tradicionales y tratando de mejorarlos. La manufactura esbelta, una rama del pensamiento esbelto, consiste en utilizar un enfoque de línea de montaje para hacer lo mismo de una manera más eficiente.
El objetivo de la fabricación esbelta es producir la mejor calidad y la mejor cantidad de un producto en el menor tiempo posible.
Kaizen en la manufactura esbelta
Kai-Zen o “cambio a mejor” es el mantra de la manufactura esbelta. Se trata de un proceso continuo y no de una sola vez. Es un proceso en sí mismo.
Al centrarse efectivamente en la mejora de la eficacia de los procesos subyacentes y en la mejora del rendimiento, se recogen las recompensas financieras.
Es como tener una medida y una “prueba” de su éxito. Al aplicar la ciencia, la resolución de problemas intuitiva y creativa, el análisis y el escrutinio a los procesos empresariales, se aumenta el control de los acontecimientos, los pasos y los resultados.
Impulsa la excelencia del rendimiento de su empresa a nuevas cotas. La fabricación ajustada le llevará hasta allí. La combinación de este enfoque con la disciplina y el rigor de la gestión de procesos y las herramientas de mejora de los procesos empresariales, como Six Sigma, aumenta el impacto y la eficacia.
Los tres pilares de fuerza de estos dos enfoques empresariales son:
- Orientación al cliente, actividad centrada y dirigida, proceso de valor añadido y resultado
- Eficacia y Eficiencia.
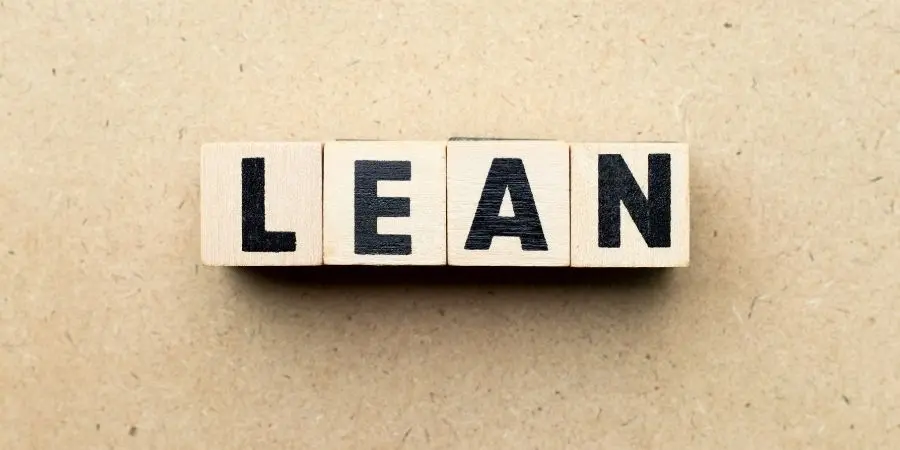
¿Cuáles son los 5 principios del pensamiento esbelto?
Los cinco principios de la manufactura esbelta son los siguientes:
5s -SORT- (SIERI). Como su nombre indica, se trata simplemente de colocar en el espacio de trabajo las herramientas/equipos que se necesitan a diario. Cualquier herramienta innecesaria se elimina de este espacio.
Fase 2 ORDENAR (SEITON). Aquí es donde cada pieza de equipo/herramienta tiene un lugar fijo en su área de trabajo. Todas las herramientas deben ser accesibles de forma rápida y eficaz, eliminando así la pérdida de tiempo.
Este proceso debe pensarse primero y discutirse con los trabajadores para asegurarse de que se cubren todas las áreas. Es algo más que una operación de limpieza rápida. Es el comienzo de un viaje lean.
Fase 3 – LIMPIEZA/SHINE (SEISO). Esto parece de sentido común pero, de nuevo, es un enfoque sencillo y de sentido común, pero debe hacerse a diario.
Después de cada día, las herramientas y los equipos deben guardarse en su lugar correcto (elimina los robos y la pérdida de equipos) y acelerará los procesos para el día siguiente. Todos los empleados deben tener esta mentalidad, ya que una mano de obra dedicada es primordial para que el proceso lean comience y mantenga su recorrido.
Es necesario establecer turnos de limpieza y repartir la responsabilidad de las áreas del centro de producción y gestionarlas adecuadamente.
Fase 4 – ESTANDARIZACIÓN (SEIKETSU). Hay que estandarizar todas las áreas. Como se ha mencionado anteriormente, hay que asignar responsabilidades a las personas y gestionarlas adecuadamente.
Si se aplica correctamente, los trabajadores se sentirán identificados y comprenderán por qué se aplican estos nuevos procedimientos, por lo que querrán participar en este proceso de mejora continua.
Fase 5 – MANTENIMIENTO (SHITSUKE). El proceso de convertirse en lean no es un proceso de una noche ni un ejercicio de tres meses. Se trata de un programa en constante cambio que hay que abordar constantemente y modificar de vez en cuando.
Hay que mantenerlo, de lo contrario la empresa se considerará ajustada cuando en realidad está en peor situación que antes.
Mantener una cultura y una actitud lean es lo que separa a un líder del mercado del resto. Con la introducción de las 5S mencionadas, las empresas estarán en el primer peldaño de la escalera para convertirse en lean.
Sin embargo, es importante que la dirección y los trabajadores no vean las 5S como una actividad de limpieza, es mucho más que eso.
Es una forma sencilla de conseguir que las personas trabajen de forma más eficiente y reduzcan los residuos.
¿Cuáles son las herramientas de la manufactura esbelta?
Los conceptos de manufactura esbelta comprenden muchas herramientas y conceptos. Cada uno de los conceptos tiene sus propias ventajas y se emplea en función de las necesidades de una unidad de fabricación.
A continuación se presentan seis de los más importantes:
Fabricación celular
Este enfoque hace hincapié en la disposición de todos los equipos y puestos de trabajo en función de los diferentes procesos, situados muy cerca de la producción de un grupo de productos similares. Su objetivo es reducir el tiempo del ciclo y los inventarios para cumplir con los tiempos de respuesta de la comercialización.
Tiempo Takt
Se conoce como el “latido del corazón” del cliente. Se refiere a la media a la que una empresa debe fabricar el producto o realizar la transacción en función de los requisitos del cliente y del tiempo de trabajo previsto.
Takt = T/D
Donde T se refiere al tiempo disponible para el producto/servicio.
D es la demanda de la cantidad. Y T da información sobre el ritmo de producción o las unidades.
Trabajo estandarizado
Se refiere a un proceso de descripción documentada de los métodos, materiales, herramientas y tiempos de procesamiento necesarios para cumplir con el takt time para cualquier trabajo proporcionado. Este enfoque ayuda a estandarizar las tareas en todo el flujo de valor.
Flujo de una pieza o flujo continuo
Este enfoque tiene como objetivo minimizar el tamaño del lote para eliminar las restricciones del sistema. Según este principio, un producto o información se produce moviéndose a un ritmo constante de un paso de procesamiento de valor añadido al siguiente, asegurando que no haya retrasos.
Sistemas Pull y Kanban
Este enfoque permite que un proceso del cliente envíe una señal a un proceso proveedor para que fabrique un producto cuando lo necesite. El kanban es básicamente las señales utilizadas dentro de un sistema pull a través de la programación combinada con la instrucción itinerante proporcionada por dispositivos visuales como contenedores y tarjetas.
Cambio rápido/ SMED
Desarrollado por Shigeo Shingo, se trata de una metodología de tres etapas cuyo objetivo es reducir el tiempo de cambio de una máquina mediante la externalización y racionalización de los pasos. Se utilizan tiempos de cambio más cortos para reducir el tamaño de los lotes y maximizar el “justo a tiempo”.
El cambio rápido reduce el tiempo de preparación, mejorando así la flexibilidad y la capacidad de respuesta a los cambios del cliente.
Diríjase a una empresa de consultoría de manufactura esbelta para saber qué herramienta sería adecuada para su unidad de fabricación.
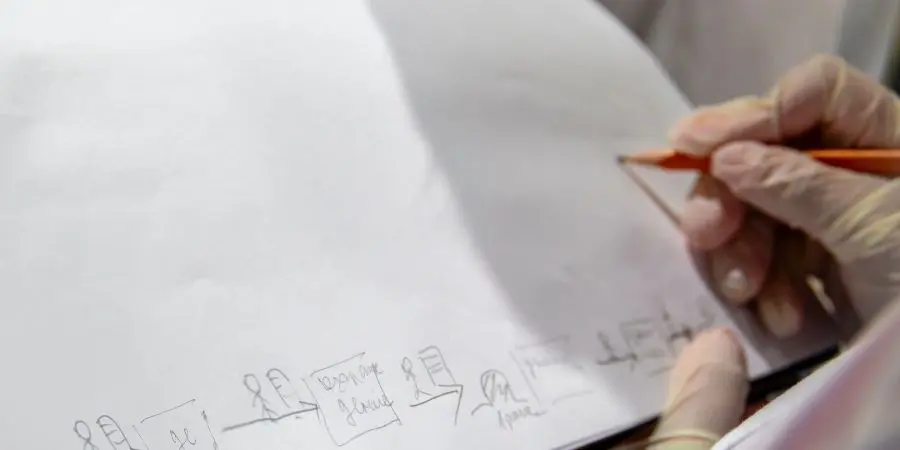
¿Cuáles son los beneficios de la manufactura esbelta?
La manufactura esbelta es una filosofía o una mentalidad, no una estrategia. Para que funcione correctamente, debe haber un deseo de aceptar el cambio.
Sé que muchas empresas son obstinadas y tienen sus costumbres fijas. Se puede garantizar que un negocio que no es adaptable no sobrevivirá mucho tiempo. Me encanta el hecho de que un cambio, o una sugerencia, pueda hacer rodar la pelota.
Con unas pocas pinceladas para guiar por dónde rueda la pelota, toda una empresa puede cambiar muy rápidamente.
La manufactura esbelta trae consigo un nivel de moral mucho más alto en el lugar de trabajo. Se anima a todo el mundo a aprender sobre el “Kaizen”, que es el proceso de mejora continua.
Si todo el mundo asume que lo que se está haciendo es la mejor manera de hacerlo, entonces se tiene una moral baja y, como resultado, empleados de bajo rendimiento. Sin embargo, si la gente siempre busca la manera de mejorar la forma en que se hacen las cosas, entonces hay un verdadero sentido de propiedad y orgullo.
He visto muchas veces lo importante que puede ser esa moral en todos los entornos, desde uno de fabricación hasta los talleres e incluso las oficinas.
Por supuesto, el beneficio real para la empresa cuando se aplica la manufactura esbelta son las ganancias monetarias. He realizado varios análisis de coste-beneficio basándome sólo en algunas de las sugerencias de los empleados de diferentes industrias, y hay literalmente millones de dólares que se tiran a la basura cada día.
Una gran empresa tiene el potencial de ahorrar cientos de miles de dólares cada año mediante unos pequeños cambios, pero tiene que estar dispuesta a hacerlos.
Creo que también debería haber un beneficio para los que sugieren los cambios. Si realmente se quiere ver una acción rápida y emprendedora, hay que recompensar a los que proponen una buena sugerencia y planifican su aplicación. Realmente es una situación en la que todos ganan: tanto el empleado como el empleador se benefician.
La manufactura esbelta también es beneficiosa en la vida personal, aunque sea algo tan básico como entender qué se puede cambiar y qué se puede eliminar para obtener mejores resultados.
Recomiendo encarecidamente a la gente que investigue sobre la competitividad y la manufactura esbelta: mejorará su forma de pensar y su rendimiento a un nivel que no habría creído posible.
Ejemplos de manufactura esbelta
La manufactura esbelta puede aplicarse a cualquier industria o negocio. Por ejemplo, Toyota ha hecho importantes incursiones en la industria del automóvil, mientras que Dell ha adoptado la manufactura esbelta para ser líder en la industria de la informática.
Sin embargo, la manufactura esbelta es especialmente adecuada para las empresas de fabricación que tienen que hacer grandes volúmenes de productos, y/o productos que requieren altos niveles de calidad y fiabilidad. El concepto de manufactura esbelta es un ejemplo de estrategia de mejora que puede aplicarse a cualquier organización.
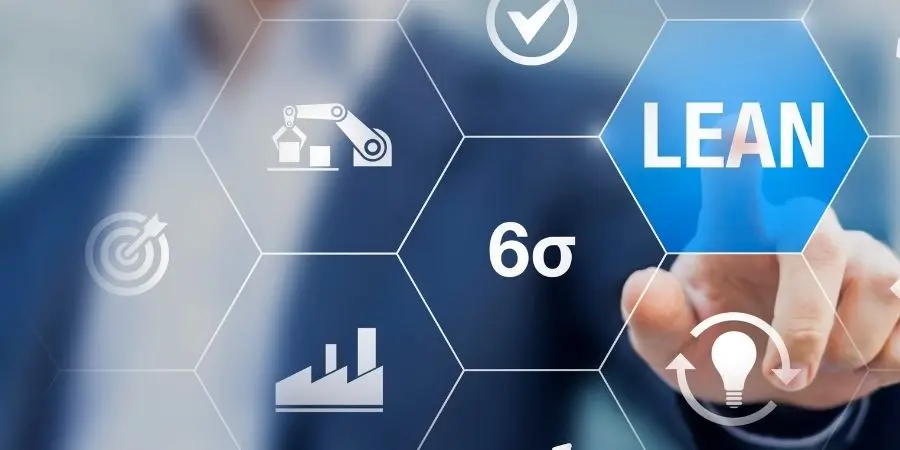
¿Cómo aplicar la manufactura esbelta en una empresa?
La manufactura esbelta está siendo utilizada por empresas de todos los tamaños.
Aunque ha tardado unos años en convertirse en la corriente principal, las historias de éxito de las medianas y grandes empresas han hecho que la manufactura esbelta llegue hasta las organizaciones más pequeñas.
La mayoría de las grandes empresas emplean a unos pocos expertos en lean. Muchas empresas medianas y la mayoría de las pequeñas no cuentan con expertos en manufactura esbelta en la empresa.
Es habitual que unos pocos individuos hayan asistido a un seminario de manufactura esbelta o hayan leído algunos libros, pero carecen de la experiencia necesaria para desarrollar una hoja de ruta.
La razón por la que la mayoría de los cursos y seminarios no enseñan una “hoja de ruta” es porque las herramientas se aplican mejor a los problemas o cuellos de botella, en lugar de forzar el uso de la herramienta en la oportunidad.
Por ejemplo, una máquina que se pone en marcha una vez a la semana en 30 minutos probablemente no justifica una semana de actividad SMED.
Sin embargo, se puede utilizar una hoja de ruta con sentido común. La manufactura esbelta ha sido denominada “manufactura de sentido común”, aunque no siempre es una “práctica común”.
Hoja de ruta de la manufactura esbelta:
- Formar un equipo (mezcla de manufactura esbelta y experiencia empresarial relevante)
- Desarrollar un canal de comunicación y retroalimentación para todos
- Reunirse con todos y explicar la iniciativa
- Empezar a formar a todos los empleados (visión general de Lean, 8 residuos, operaciones estándar, Kaizen, RCPS, PDCA)
- Análisis de las instalaciones – Determinar el desfase entre el estado actual y un estado “lean”
- 5S – Es la base del lean. La organización del lugar de trabajo es fundamental para cualquier iniciativa lean
- TPM – Comenzar el mantenimiento productivo total desde el principio (se utiliza en todo el lean)
- Mapeo del flujo de valor – Determinar los residuos en todo el sistema
- 7 (u 8) Identificación de residuos – Se utiliza con el mapeo del flujo de valor para identificar los residuos del sistema
- Mapeo de procesos – un mapa más detallado de cada proceso
- Tiempo de espera – determinar la necesidad de producir en todos los procesos y equipos
- OEE y 6 Pérdidas – determinar las pérdidas en todos los procesos y equipos
- Balance de líneas – Utilizarlo si es necesario con la cadencia y la OEE
- SMED – reducir los tiempos de preparación para reducir el tiempo de ciclo, la cantidad de lotes y los costes.
- Análisis de flujo pull/de una pieza/de flujo continuo – utilizar kanban y supermercados
- Analizar la calidad en la aplicación de origen – la mala calidad se detiene en el origen
- Implantar ideas a prueba de errores
- Fabricación celular/Mejora de la disposición y el flujo – Analizar las instalaciones y cada proceso
- Desarrollar operaciones estandarizadas – simultáneamente con SMED, balance de líneas, flujo, layouts
- Kaizen – seguir mejorando las operaciones, dando prioridad a los cuellos de botella dentro del sistema.
El plan de implementación específico debe desarrollarse a partir del análisis de las instalaciones.
El análisis identifica áreas de oportunidad en todas las áreas de la empresa, incluidas las ventas, el servicio, la ingeniería, el mantenimiento, la producción, la calidad, los envíos y las funciones administrativas.
Algunos proyectos de manufactura esbelta dentro de una iniciativa lean requieren las herramientas de seis sigma para encontrar las respuestas de mejora.
El equipo de manufactura esbelta debe estar capacitado para entender cuándo deben complementarse las herramientas lean para resolver el problema o maximizar la mejora.
Los eventos kaizen pueden utilizar todas las herramientas lean (y algunas herramientas six sigma) para alcanzar el objetivo del equipo.
Los eventos kaizen se llevan a cabo de forma continua para alcanzar un estado de “lean”. Por ejemplo, un proceso puede necesitar una mejora rápida del rendimiento. La campaña kaizen podría incluir un análisis SMED (intercambio de troqueles en un minuto) y OEE.
El kaizen podría tener como objetivo reducir el tiempo de preparación de 80 minutos a 60 minutos en 4 días.
Es importante mantener una visión empresarial con el análisis y la hoja de ruta. No se debe mejorar una sola operación a expensas de todo el sistema.
Por ejemplo, si un cuello de botella se produce en el proceso B, mejorar el proceso A antes del B sólo perjudica al sistema. Un ejemplo a mayor escala es mejorar el rendimiento si el envío no puede manejar el volumen.
Aunque muchas mejoras provocan cuellos de botella en otros lugares, forzar un problema mayor conocido no suele ser una buena idea.
La hoja de ruta anterior es sólo un ejemplo. Podría mostrarse con muchas variaciones diferentes. Sin embargo, hay una secuencia lógica en muchas de las herramientas.
El mapeo del flujo de valor se realiza casi siempre en las primeras fases del proceso. El sistema de las 5S proporciona una base para la mayoría de las demás herramientas. El TPM es amplio y desempeña un papel importante en la mejora de la OEE, por lo que debe iniciarse pronto.
La clave es tener un plan y empezar. El camino hacia el lean no será recto y nunca termina. No deje que la búsqueda de la perfección le impida ser “mejor” hoy.
Ventajas de la manufactura esbelta
Si su empresa sigue las técnicas de manufactura esbelta, se beneficiará de las siguientes maneras para prestar un mejor servicio.
- Ahorro de espacio: La reorganización del taller para que el lugar de trabajo sea más eficiente también ayuda a ahorrar mucho espacio. La idea es diseñar el taller de forma que todas las herramientas estén al alcance de los trabajadores para que no pierdan tiempo trabajando.
- Ahorrar tiempo: La cadena de montaje puede tener ciertos procesos innecesarios simplemente porque no se ha pensado bien en su diseño. Si se eliminan los procesos innecesarios, el trabajo puede completarse en el menor tiempo posible. Del mismo modo, si todas las herramientas se colocan en su propia ranura, será muy fácil encontrarlas.
- Mejora de la calidad: Si utiliza las técnicas de manufactura esbelta, podrá eliminar los errores en el proceso de producción, mejorando así la calidad de los productos que fabrica.
- Ahorro de dinero: Podrá realizar su trabajo en un espacio bastante compacto si reorganiza los diferentes procesos de trabajo para aprovechar al máximo el espacio. El hecho de que sus empleados puedan trabajar de forma más eficiente que antes también le ayudará a reducir los costes de mano de obra. También ahorrará dinero, ya que se rechazarán menos productos.
- Mayor competitividad: Dado que su empresa se centra en la capacitación de los empleados y en la mejora continua, siempre podrá seguir siendo competitiva incluso en un mercado difícil.
Descarga o imprime la versión de Manufactura esbelta en PDF y consúltala donde quieras en el siguiente link: