Autor: Bob Jenkins
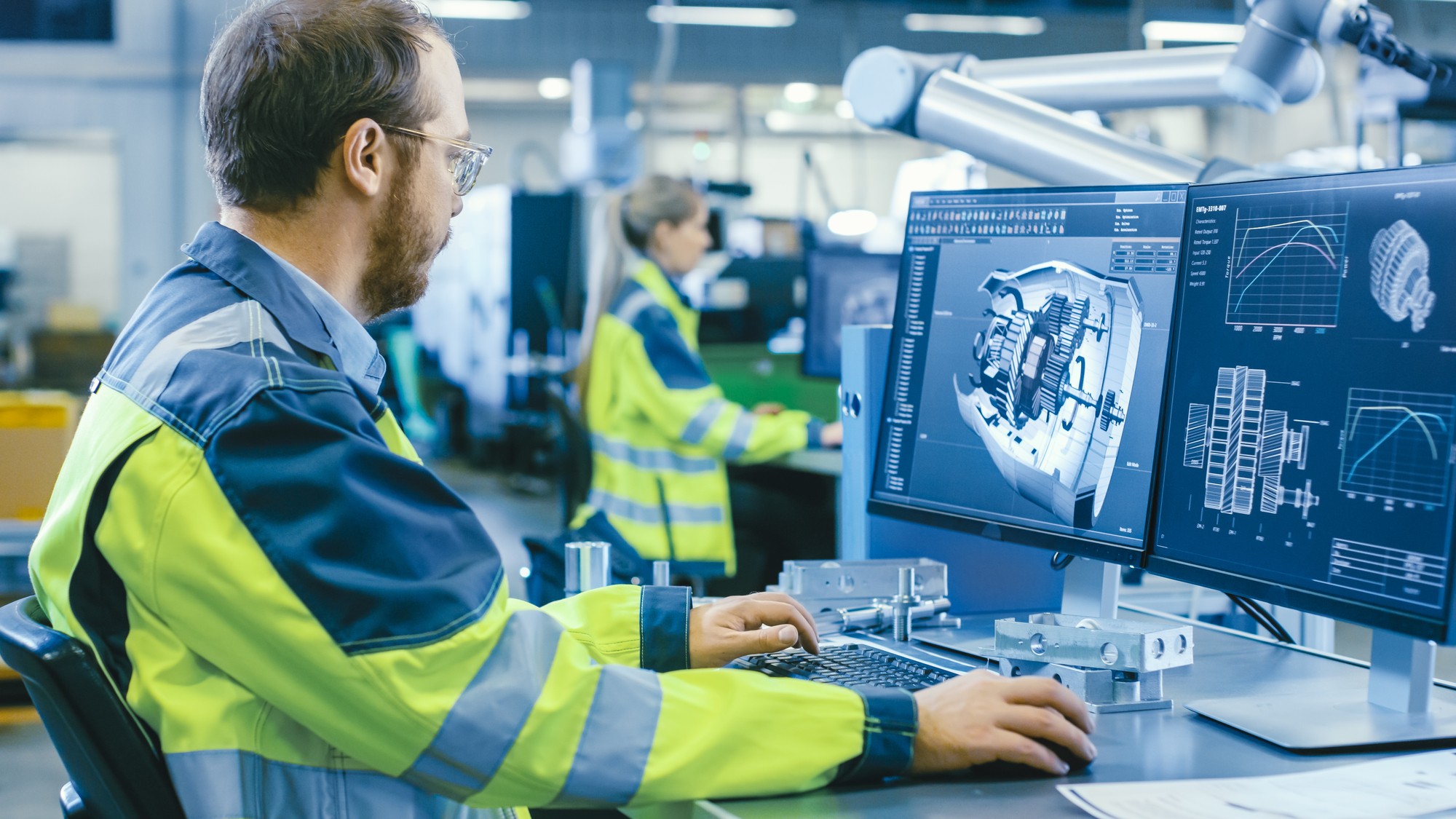.jpg.aspx?width=300&height=168)
Para fortalecer los diseños y reducir las fallas, IATF 19649:2016 requiere que los ingenieros de diseño tengan competencias de diseño para fabricación (DFM) y diseño para ensamblaje (DFA). Este estándar proporciona una mayor protección contra errores y mejora significativamente la fabricación. Las auditorías consistentes de terceros según la Sección 8.3 del estándar y el cuestionamiento de los antecedentes de DFM y DFA de los diseñadores continúan mejorando el proceso.
Los diseñadores pueden centrarse en la fabricación eficiente en lugar de preocuparse por la cantidad de errores. Si no puede generar un error, no obtendrá tantos errores. El análisis de efectos y modos de falla de diseño (DFMEA) puede volverse más efectivo al considerar más a fondo los posibles errores durante la fabricación. Anteriormente, los únicos diseños que FMEA tenía en mente eran: “Teniendo en cuenta los materiales que utilizamos y los métodos de construcción, ¿qué podría salir mal?” Así es, “¿Qué pasará con los clientes?” posición. No tiene nada de malo, pero otros clientes también son importantes.
Trabajando hacia cero defectos
En otras palabras, cuando W. Edwards Deming llegó por primera vez a Ford Motor Company después de su paso por Japón, alcanzó un nivel de cero defectos que se consideraba inalcanzable. Cuando Don Peterson lo invitó a ayudar a mejorar Ford, la industria estaba midiendo las garantías en R/1000. Cuando la medición pasó a partes por millón (PPM) y las fallas aceptables se redujeron en un factor de 1000, nadie creyó que se pudiera lograr. Hace unos años, GM empezó a utilizar PPB (partes por mil millones). “No quiero ver defectos”. El concepto de cero defectos es real.
Al principio, cero defectos se consideraba un mito. El Toronto Sun-Times publicó un artículo sobre cero defectos y cómo es imposible. Hablaron de que IBM había pedido 10.000 placas de circuitos a Japón. El artículo utilizó la práctica común (en ese momento) de citar MIL Spec 105D. Este estándar proporcionó tasas de falla dentro del lote que se consideraron aceptables. Afirmó además que “la presencia de tres placas defectuosas en un lote de 10.000 lotes se considera aceptable”.
Cuando el pedido completo llegó a IBM, abrieron la caja que contenía 10.000 placas de circuito y encontraron una nota. Fue escrito así, “Como japoneses, es difícil para nosotros entender las prácticas comerciales norteamericanas, pero en el paquete se incluyeron tres placas defectuosas y se envolvieron por separado. Espero que todo esté bien”.
Expansión con GD&T
A partir de esa experiencia, sabemos que lograr cero defectos es una forma de pensar. Pero no quiero desviarme del verdadero objetivo de este breve blog. Nuestro objetivo aquí es ampliar DFM. Claro, es mejor incluir factores que eviten la creación de piezas defectuosas, pero también debes incluir factores que den a la fabricación la oportunidad de variación si te lo puedes permitir. Para incorporar esto completamente como una opción de diseño, todos los diseñadores deben comprender las dimensiones y tolerancias geométricas (GD&T).
GD&T, en su forma más obvia, tiene una especificación de orificio cuadrado versus redondo. Si eso no le parece obvio, tomar la clase de Fundamentos de GD&T es el camino a seguir. El lenguaje de GD&T permite a los diseñadores “darle sentido” a sus dibujos de una manera consistente en todas las industrias. Las especificaciones y regulaciones de dibujo uniformes reducen las conjeturas, las controversias y las suposiciones hechas durante el proceso de fabricación, lo que lleva a cero defectos.
Sin embargo, para mantener la solidez, GD&T debe incorporarse específicamente en la próxima versión de la norma IATF 16949, junto con los requisitos DFM y DFA para las competencias de los ingenieros de diseño. Una vez que los ingenieros de diseño aprendan cuánto pueden contribuir a la fabricación y qué tan buenos son los productos, todos querrán pasar a GD&T.
Principalmente GD&T
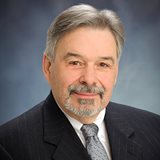
categoría: Mejora continua, GD&T, fabricación, control de calidad.