Autor: Andy Nichols
.jpg.aspx?width=300&height=200)
En la fabricación, necesita medir o probar sus productos fabricados porque los resultados variarán, pero no desea exceder las especificaciones, lo que resultará en costos adicionales, pérdida de tiempo e incluso insatisfacción del cliente.
¿Sabías que también existe variación en el acto de medir los productos que fabricamos? Como ocurre con cualquier proceso de fabricación, existen varias fuentes de variación y vale la pena tomarse el tiempo para comprenderlas. Después de todo, nadie quiere tirar miles de dólares en productos porque las medidas fueron incorrectas.
Comprender las variaciones
Usando un diagrama de Ishikawa (también conocido como espina de pescado), puedes ver que la variación es causada por:
-
Hombre: generalmente se encuentra usando Gauge R&R
-
Método: generalmente se descubre a través del medidor R&R.
-
Materiales – omitidos por el momento
-
Mecánico – equipo de medición
.jpg.aspx?width=500&height=179)
Entonces, ¿cómo saber cuánta variación es inherente al equipo que mide su producto? El estudio de la variación se llama “calibración” y muestra qué tan bien se desempeña el equipo a lo largo del tiempo. Usted puede averiguar qué hacer. A diferencia de la simple “verificación” de un equipo, la ciencia de la calibración utiliza métodos matemáticos para evaluar la cantidad de variación presente comparándola con un valor finito.
Puede utilizar el diagrama que se muestra arriba al considerar el proceso de calibración. Al ser una medida diferente, sabemos que lo mismo afecta la variación detectada. Esta vez se realizará en un instrumento de medición y no en un producto que se esté fabricando. Las organizaciones suelen enviar algunos de sus equipos de medición a un proveedor de servicios de calibración (laboratorio), que luego suele recibir la certificación (ISO/IEC 17025). Esta certificación demuestra que el laboratorio comprende las variaciones inherentes al proceso de calibración. Estos incluyen el equipo utilizado para calibrar el equipo del laboratorio, su personal, el entorno en el que se realizó la calibración, etc. El análisis matemático de laboratorio tiene en cuenta dos categorías de variación conocidas como “incertidumbres”.
Debido a que los laboratorios no pueden estar 100% seguros al medir valores exactos (debido a diversas influencias), valores matemáticos (conocidos como incertidumbres “Tipo A”) y otros valores estimados, el “Tipo A” informa resultados basados en las asignaciones conocidas. (también conocido como). Incertidumbre tipo B”). Este valor derivado matemáticamente permite a los laboratorios informar los resultados de la calibración con cierto grado de confianza, indicado por una “k” y generalmente un número de 2 o 3. Estos corresponden a la desviación estándar “sigma” (σ), que representa: Nivel de confianza de la precisión informada. Por ejemplo, k = 2 es 95%, k = 3 es 99%.
¿Porque es esto importante?
Los resultados de laboratorio deben usarse para guiar el próximo retiro y calibración de equipos planificados por una organización. Después de todo, la calibración anual que normalmente se realiza en los instrumentos de medición no tiene en cuenta el uso durante ese período. ¿Qué pasaría si la organización agregara un segundo o tercer turno de producción para fabricar piezas? La utilización del equipo ahora es mucho mayor, por lo que los retiros deberían ser más breves. Si no sabe dónde está funcionando su equipo de medición dentro de su rango de tolerancia, no puede establecer puntos de recuperación ni asegurarse de que se mantenga dentro de sus límites operativos antes de salirse de las especificaciones.
Utilice los servicios de calibración con prudencia y los resultados que obtenga beneficiarán a su organización.
-
Ahorre dinero al no tener que enviar su equipo a calibración cuando no sea necesario
-
Para evitar que las condiciones del equipo salgan de las especificaciones antes de lo esperado y provoquen fallas no deseadas, etc.
¿Qué hace la validación por nosotros?
Esta es una palabra que a menudo, y de manera algo incorrecta, se usa indistintamente con el término “calibración”. Es muy común que los operadores verifiquen el equipo de medición (micrómetros, calibradores, etc.) antes de usarlo con un dispositivo “maestro” calibrado, generalmente un bloque patrón. Esto le brinda información instantánea de que su dispositivo no está dañado o desgastado antes de usarlo. Se trata de una práctica “comprobación del estado” del dispositivo y no requiere matemáticas asociadas con el acto de calibración.
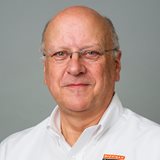
categoría: Fabricación, control de calidad.