🕑 Tiempo de lectura: 1 minuto
Los ensayos no destructivos son una solución para encontrar la resistencia de las estructuras de acero existentes y sus conexiones (como las soldaduras). La prueba de dipenetración, la prueba de partículas magnéticas y la prueba ultrasónica son varias pruebas no destructivas (NDT) realizadas para encontrar la resistencia de las estructuras de acero existentes.
Tabla de contenido
Tipos de pruebas NDT para acero estructural
1. Prueba de penetración de soldadura
La prueba de penetración de líquidos en soldaduras es la prueba no destructiva más común. Esto se debe a que es económico, versátil y requiere menos capacitación que otros exámenes de ND. La “Prueba de Penetración de Líquidos” verifica defectos de material en la superficie del acero estructural. Esta prueba también se puede utilizar en metales ferrosos y no ferrosos, materiales no porosos y no metálicos. Se aplica un líquido penetrante adecuado a la superficie que se va a probar y se deja allí el tiempo suficiente para que el líquido penetre cualquier defecto abierto en la superficie. Después del tiempo de residencia del penetrante, se elimina el exceso de penetrante que queda en la superficie. Luego se aplica un desarrollador seco o húmedo a la superficie. Este revelador actúa como secante, extrayendo algo del penetrante que ha penetrado en las aberturas de la superficie. A medida que se extrae el penetrante, se difunde en el revestimiento del revelador y forma discontinuidades en la superficie o marcas de rayones.
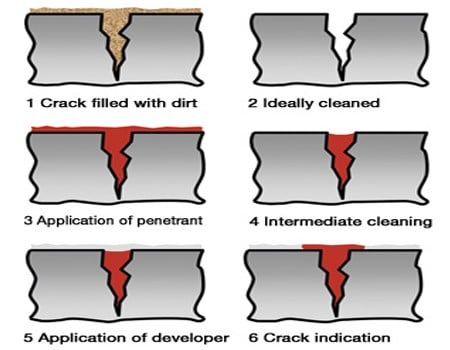
2. Pruebas de partículas magnéticas de soldaduras
La inspección por partículas magnéticas es una prueba no destructiva que detecta defectos superficiales superficiales y subterráneos en materiales ferromagnéticos. Esta prueba es un método muy eficaz para localizar fracturas superficiales y defectos leves del subsuelo, como grietas de material magnético, porosidad, envolturas en frío y falta de fusión de la pared lateral de la soldadura. La parte a probar se magnetiza con la ayuda de algún sistema de magnetización y luego se aplican algunas partículas magnéticas a la superficie de prueba. Las líneas de campo magnético viajan perpendiculares a la dirección de la corriente. Fugas de flujo magnético debido a la presencia de discontinuidades superficiales o subterráneas. Estos campos marginales atraen partículas magnéticas que se aplican a la superficie de prueba. La acumulación de partículas en la superficie indica fallas o discontinuidades en la superficie de prueba.
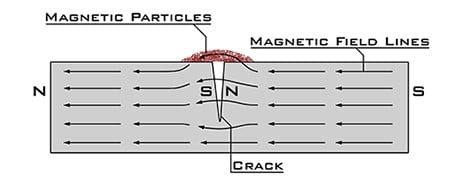
3. Medición de espesor por ultrasonidos
La medición ultrasónica de espesores es útil para inspeccionar el espesor del acero estructural. Las mediciones de espesor son esenciales en muchas industrias para monitorear la corrosión, la erosión y el daño. La detección de pérdida de metal debido a la corrosión, la erosión o el daño es esencial para garantizar la seguridad y el funcionamiento continuos del elemento o la estructura inspeccionados. Un medidor de espesor ultrasónico funciona midiendo con precisión el tiempo que tarda un pulso acústico, generado por una pequeña sonda llamada transductor ultrasónico, en atravesar una muestra y reflejarse en una superficie interna o una pared distante. A partir de esta medición, el espesor de la muestra se calcula y se muestra en la pantalla digital.
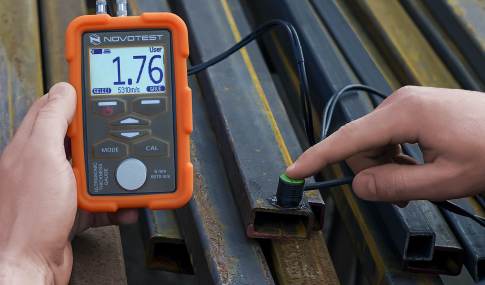
cuatro Inspección ultrasónica de soldaduras y chapas
La inspección ultrasónica es la técnica de propagación de ondas ultrasónicas a través del material que se está inspeccionando. En esta prueba, se transmiten ondas ultrasónicas al material para detectar fallas internas o examinar las características del material. La onda del pulso ultrasónico es altamente direccional y viaja a través del medio bajo prueba hasta que encuentra un límite con otro medio (como el aire). En este punto vuelven a su origen. Al analizar estos reflejos, puede medir el espesor de la muestra o encontrar evidencia de grietas u otros defectos internos ocultos. Esta prueba se puede realizar en soldaduras y secciones de acero estructural para detectar defectos de material.
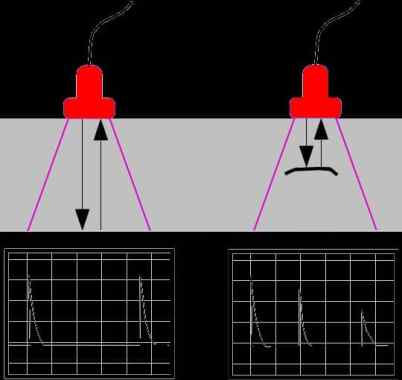